Highlighting the characteristics and benefits of micro Electron Beam and Laser-in-Vacuum welding.
Our expertise at FOCUS is advanced welding, drilling, and surface modification of complex pieces at the micron scale.
Laser and micro Electron Beam systems can both produce sub 50µm spots with high power densities, but selection of an ideal welding technique is determined by the material(s) of the work piece. For insulating and magnetic materials, welding with electron beam can often be challenging due to surface charging and/or beam distortion. The FOCUS LaVa system brings the power of laser welding into a vacuum environment, enabling ultra clean deep penetration welding at much lower temperatures than at atmosphere. Since the boiling point of materials is pressure dependant, temperatures up to 1000°C lower than under atmospheric conditions are achieved when operating the laser under vacuum conditions. Welding at lower temperatures limits thermal cycling and reduces distortion, whilst also minimising sputtering due to a stable keyhole formation. Minimising initial investment costs and optimising cycle times, low power lasers – typically 500W – 2kW – and an easily achievable vacuum can be used for micron welding under vacuum.
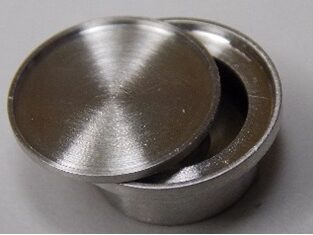
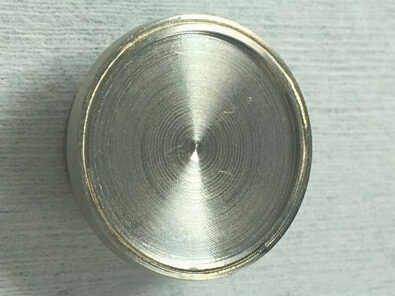
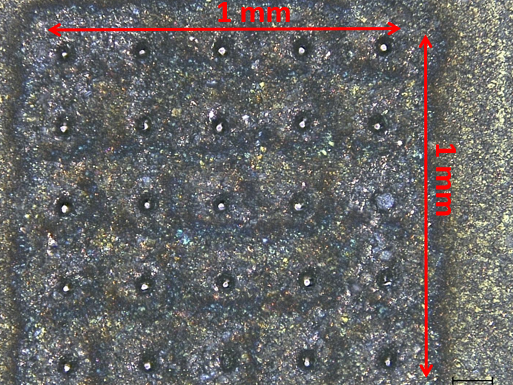
Laser welding efficiency is limited when the workpiece reflects initially a large percentage of the laser light, limiting induced power and making it hard to form the keyhole. The reflectivity of the material can be a problem when working with precious metals or joining dissimilar materials, where a well-adjusted temperature gradient across the material interface is required to minimize formation of intermetallic phases. For these materials, the FOCUS Micro Electron Beam (MEB) is the preferred solution and is tried and tested in the aerospace and space sectors.
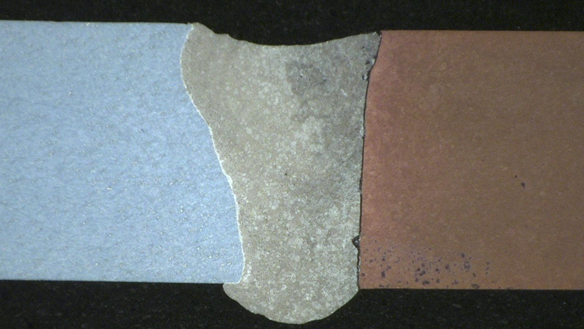
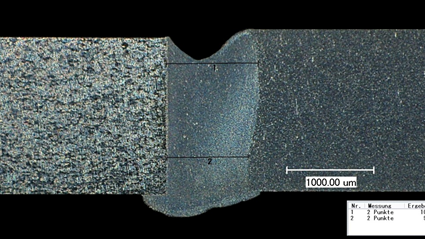
The biggest differences of an Electron Beam source are that the energy absorption is independent of the workpiece material and that the operator is able to precisely vary the power from 50W to 2KW. A similarly broad power range with a laser platform would require multiple laser sources and would still not be able to match the single Watt, fine power control of an Electron Beam. A further benefit of the Electron Beam for some operators is that the spot size can be continuously varied from 25µm to greater than 1 mm with large 100 kHz deflection frequencies, when compared to 1 kHz for regular laser source mirrors.
For those looking for the ultimate solution in materials flexibility, combining both source types into a single system is the preferred solution. With our experience in both forms of in-vacuum welding FOCUS has an integrated dual-source platform for a research institute to study a wide range of joining and machining technologies.
Our unrivalled experience at FOCUS in electron beam and Laser-in- Vacuum welding allows us to advise and support our customers when considering the best welding tool configuration for their needs, optimising performance, cycle times and cost.
Why not contact us to learn more about Laser-in-Vacuum and Micro Electron Beam welding ?