FOCUS Welding, as part of SPECS GmbH and the LAB14 Group, is a globally operating company whose expertise lies in the field of micro-beam welding. In addition to the development and manufacture of high-precision electron beam and laser in-vacuum systems for welding, drilling and surface modification, we also offer high-performance and competitive contract manufacturing at our location in Hünstetten. Our employees, with their extensive know-how and many years of experience in the field of EB and LaVa welding, look forward to discussing your welding task with you.
Electron beam welding – and more recently laser-in-vacuum (LaVa) welding – has been used for many decades wherever maximum reliability of the weld seam is required. The unrivaled quality allows the weld seam to withstand the heaviest loads, especially in the areas:
- Sensor technology
- Aerospace engineering
- Automotive
- Electromobility
- Nuclear energy
- Medical technology
- R&D
- and much more
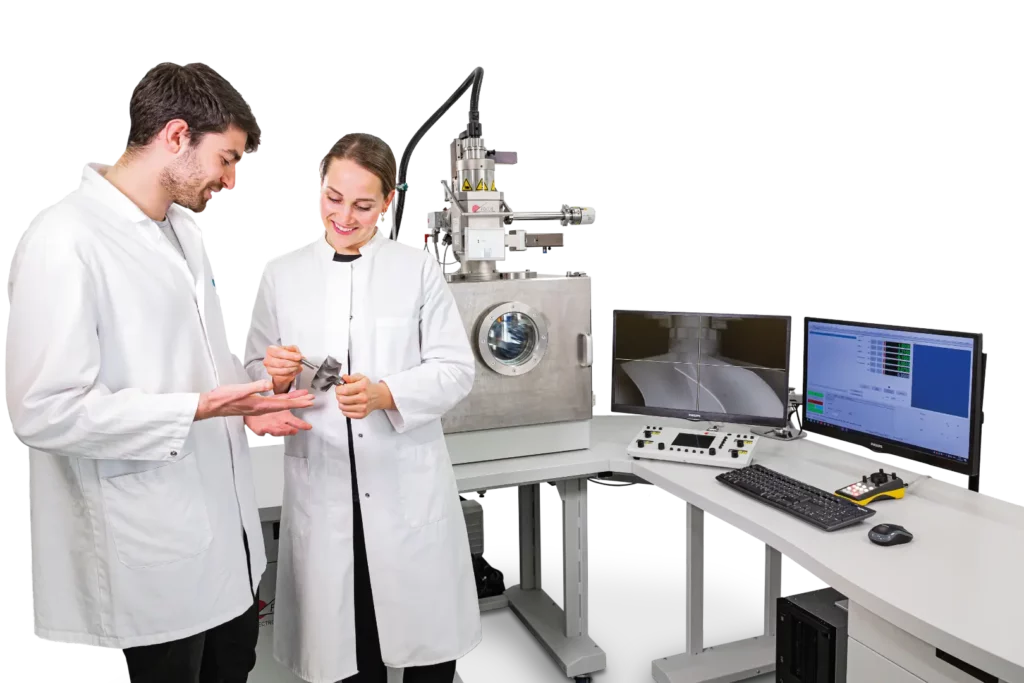
These are ideal areas of application for our Focus micro-beam welding systems. With our machines it is possible to create distortion-free connections with the least amount of energy input. Especially with difficult workpiece geometries, a wide variety of materials and material combinations.
Our job shop services at a glance:
Advice: we advise you on the design of the workpieces to be joined in order to achieve the desired welding result cost-effectively and quickly.
Feasibility: we will find a solution for your task if it is physically feasible. We have various systems and technologies at our disposal for this purpose. With the latest machine, ELWIS, we can find out whether EB or LaVa welding is the appropriate process.
Jig construction: the smaller the part to be welded, the more important the jig becomes. Our many years of experience help us to optimally design the workpiece holder.
Beam welding: the machines available to us allow us to weld in vacuum with both the electron beam and the laser. These can be individual pieces or smaller series. We also find a solution for large series.
Quality assurance: we can demonstrate and apply numerous certificates of competence and procedural tests to ensure quality at all times.
We offer the following test methods:
In-situ SEM control: all FOCUS electron beam welding machines are equipped with SEM (Scanning Electron Microscopy) for in-situ quality control as standard. This allows the workpieces and the weld seam to be checked immediately after welding.
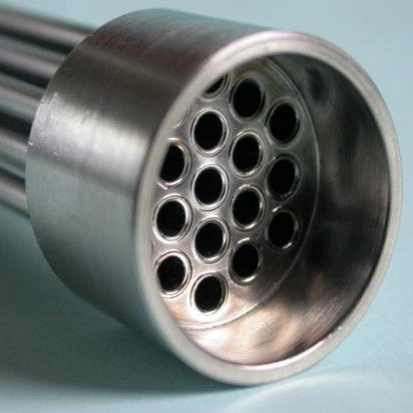
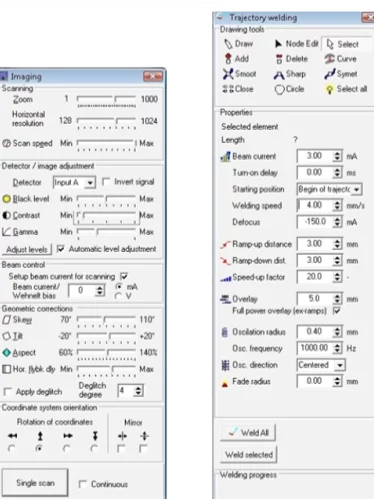
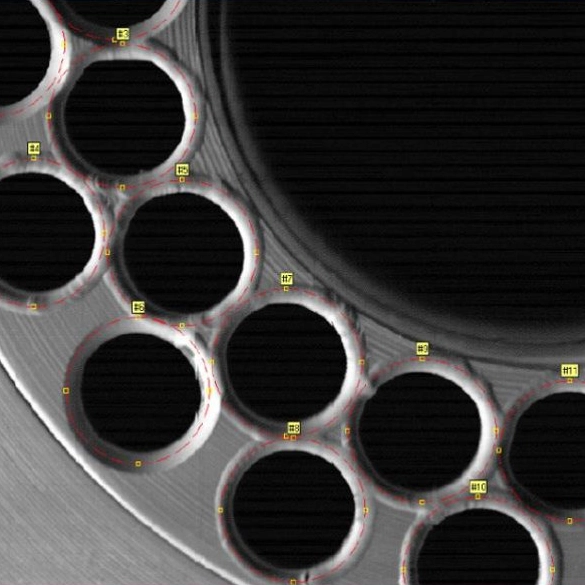
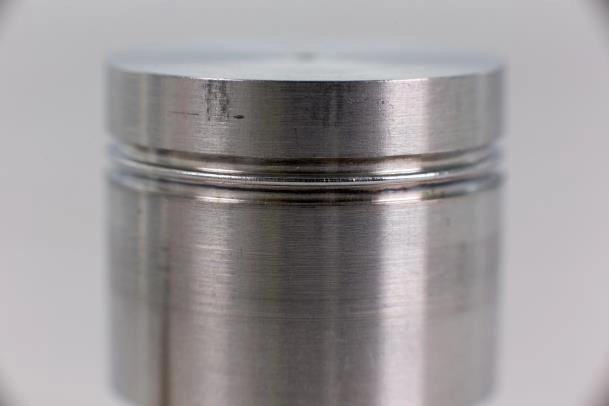
Visual inspection: using a visual inspection, weld seams can be checked for external defects such as cracks, spatters, edge offsets, pores on the surface and many more.
Macro section: the light microscopic image of a macro section provides information about the heat penetration zone, the weld seam width, the weld seam depth, the upper and lower bead, the porosity, possible crack formation and much more.
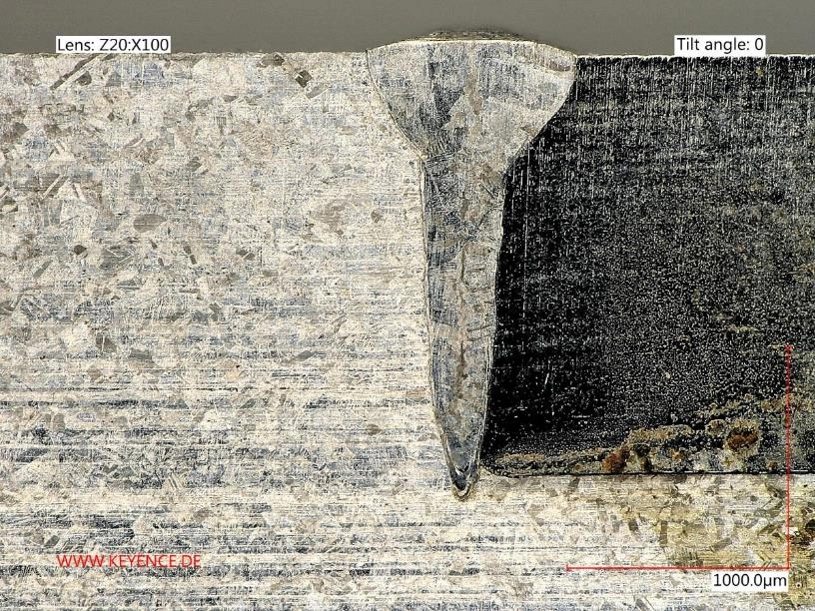
Non-destructive testing: e.g. dye penetrant testing PT or magnetic powder testing MT
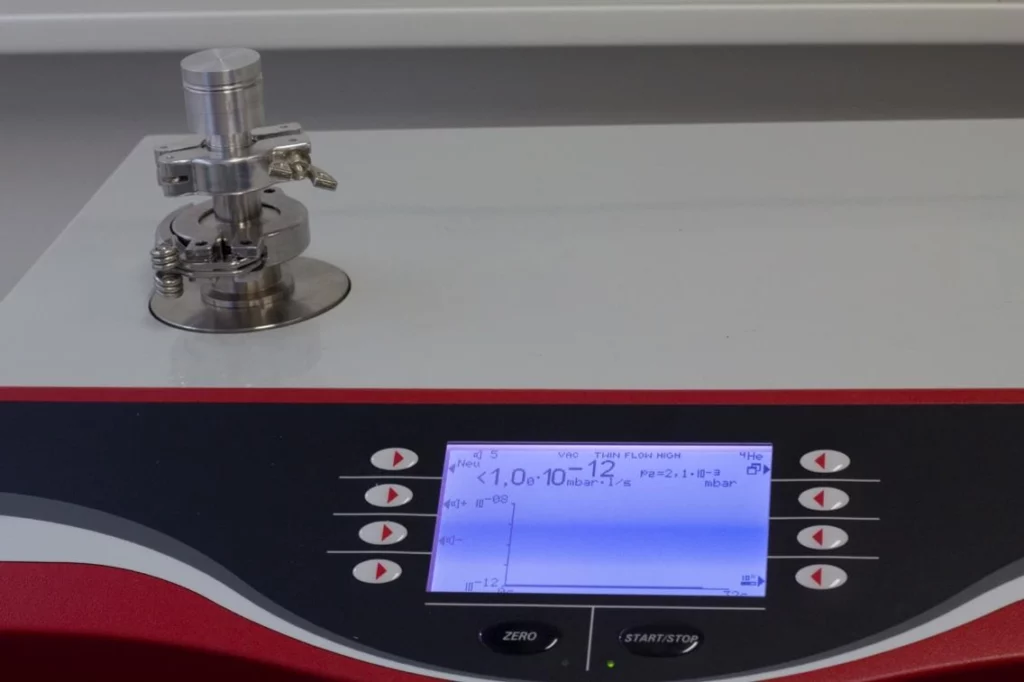
Leak rate investigation: the tightness of a weld seam can be examined using a helium leak detector. The leak rate can be determined up to a value of < 1*10-11 mbar l / s.
We carry out hardness tests, impact tests, X-ray analysis, tensile tests and microsections together with our external partners.
Here are just a few examples from our contract manufacturing:
- optical probes made of stainless steel for the food industry
- Stainless steel pressure sensor housing
- Stainless steel/titanium/molybdenum optical probes in healthcare
- highly flexible OFHC copper strands for heat conduction in cryogenic systems
- Titanium and titanium aluminides for vehicle technology
- Nickel and nickel alloys in the nuclear industry
- Aluminum and aluminum alloys in aircraft construction
- Stainless steel/stainless steel connections (various stainless steels such as 304 (1.4301), 316L (1.4404), 316LN (1.4429))
- Connections made of high-alloy steels
- Connections made of chrome/nickel steels
- Connections made of nickel-based alloys (Inconell, Hastalloy)
- Titanium/Kovar connections (with copper or copper/niobium intermediate layer)
- Stainless steel/Kovar (Invar/Havar) connections
- Molybdenum/stainless steel connections
- Titanium/stainless steel connections
- Titanium/titanium compounds
- Compounds made of tungsten carbide and high carbon steel
We also do individual manufacturing for electron beam welding handling tools and the development of welding processes.
For further details and orders please contact us by using the contact form or directly.